Taiyo-sha (Gifu)
Lösung des Problems des Mangels an Arbeitskräften in der Druckvorstufe durch die Einführung von PTS
Verringerung der Zahl der erforderlichen Arbeitsstunden um 80 % – von 5 auf ein 2-Personen-System
15 February 2025 17:38 Company Report
Neue Werte schaffen mit dem Thema „Die Bibliothek des Verlagswesens“ – Taiyosha, ein Unternehmen mit
das auf eine 82-jährige Geschichte im Verlags- und Druckwesen zurückblicken kann (Hauptsitz: 148-1 Kitagata, Kitagata-cho,
Motosu-gun, Präfektur Gifu; Präsident: Shigenori Omichi), führte das von der ECO vorgeschlagene Plate Transportation
System (PTS), das von ECOSYS vorgeschlagen wurde, im vergangenen Oktober das Plate Transportation System
(PTS) eingeführt, das von ECOSREE vorgeschlagen wurde, und zwar vor dem Hintergrund eines sich verschärfenden Arbeitskräftemangels. Durch
Automatisierung des Prozesses vom Stanzen und Biegen der fünf Plattentypen, die von den beiden
und Biegen der fünf Plattentypen, die von den beiden CTPs ausgegeben werden, bis hin zum automatischen Sortieren der Platten in die zehn Staplertypen, wurde die Anzahl der
die Anzahl der Berührungen der Platten durch die Arbeiter um 80 % reduziert. Dem Unternehmen ist es gelungen
die Anzahl der Mitarbeiter und die für den Plattenherstellungsprozess benötigte Zeit zu reduzieren sowie
Probleme im Zusammenhang mit den Platten zu beseitigen.
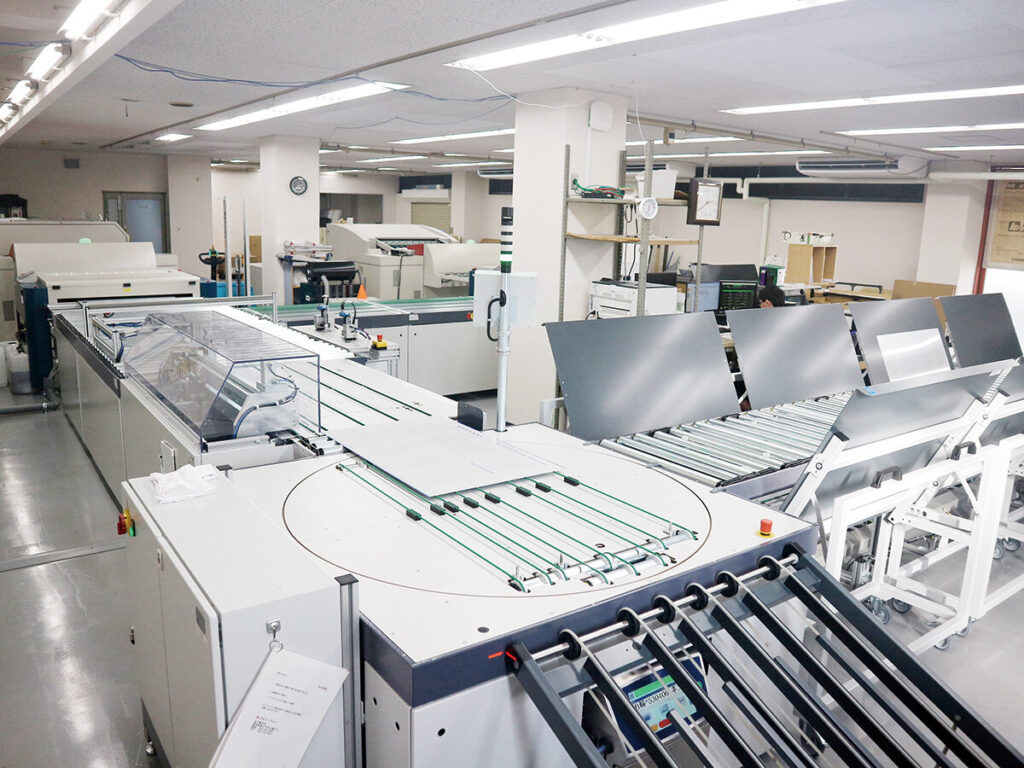
Verlagswesen + 4 neue Unternehmen
Taiyosha wurde 1921 gegründet. Das privat geführte Unternehmen war vorwiegend im Bekleidungssektor tätig und wurde erst 1943 gegründet, als sich die Kriegslage immer weiter zuspitzte. Glücklicherweise blieb das Unternehmen den Verwüstungen des Krieges entgangen und erhielt viele Aufträge, vor allem für den Druck von Telefonbüchern, nicht nur aus der Präfektur selbst, sondern auch aus Aichi und Shiga. Es handelt sich um eine alteingesessene Druckerei, die in der Wiederaufbauphase nach dem Krieg ein rasantes Wachstum erlebte.
Der größte Wendepunkt für das Unternehmen war die Einführung einer Offset-Rotationsdruckmaschine im Jahr 1967. Aufgrund der strategischen Entscheidung des Managements, „eine umfassende Neuausrichtung hin zu Druckereibetrieben mit Spezialisierung auf den Verlagsbereich vorzunehmen“, installierte das Unternehmen zeitgleich mit der Fertigstellung des Werks in Kitakata eine vollformatige A-Format-Offset-Rollendruckmaschine, für die es damals in Japan nur wenig Betriebserfahrung gab. Seitdem ist Taiyosha Publishing als Unternehmen bekannt, das weiterhin mit einem ausgeprägten Sinn für Integrität Bücher produziert.
Das Unternehmen ist auf Lehrmaterialien wie Lehrbücher, Nachschlagewerke, Firmengeschichten und Wörterbücher spezialisiert und druckt auch zertifizierte Lehrbücher. Besonders bekannt ist es jedoch für den Druck sogenannter „roter Bücher“, Sammlungen von Fragen früherer Universitätsaufnahmeprüfungen, die von Kyoikusha veröffentlicht und nach Universität und Fakultät sortiert werden. Dieses Geschäft, das einen Anteil von fast 45 % hält, macht ungefähr 23 % des Gesamtumsatzes aus.
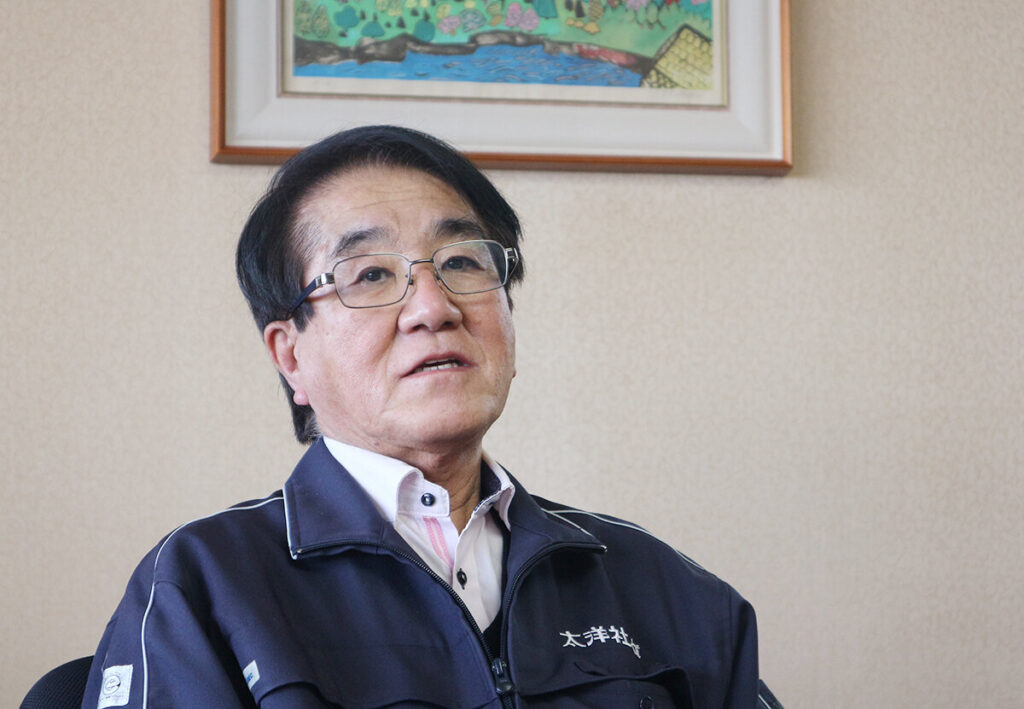
Unterdessen macht sich Präsident Daido, der sein Amt nun schon im neunten Jahr innehat, zunehmend Sorgen um die Zukunft des Druckgewerbes: „Wenn es so weitergeht, werden wir nicht mehr länger allein vom Drucken überleben können.“ Vor vier Jahren gründete das Unternehmen auf Anraten einer Unternehmensberatung vier neue Geschäftsbereiche: zwei als Erweiterungen der Druckindustrie und zwei in anderen Bereichen.
Zunächst gründeten wir in der Druckindustrie eine Planungs- und Vertriebsabteilung und begannen mit PR- und Event-Support-Aktivitäten für alle 42 Städte und Gemeinden in der Präfektur Gifu. Das zweite neue Geschäftsfeld sind Jubiläumsveranstaltungen für Firmen, Schulen, Krankenhäuser etc.
Unabhängig vom Druckgeschäft startete das Unternehmen 2021 außerdem ein Agrargeschäft. Sie züchten Shiitake-Pilze und Judasohren in Wara Town, Gujo City, Präfektur Gifu. Das andere ist die Einführung von Programmierkursen für Grundschüler. Beide Unternehmen haben mit der Diversifizierung ihrer Geschäftstätigkeiten begonnen, indem sie neue Geschäftsbereiche gegründet haben, die eng mit der örtlichen Gemeinschaft verbunden sind.
Automatische Verteilung auf 10 Staplertypen
Eine Besonderheit des Unternehmens ist sein integriertes Produktionssystem, das es ihm ermöglicht, alle Prozesse vom Satz über die Plattenherstellung, den Druck und die Bindung bis hin zur Logistik aus einer Hand anzubieten. Aus diesem Grund sind wir sehr zuversichtlich, dass wir Liefertermine einhalten können. Auf der anderen Seite war das Unternehmen mit einer Überalterung der Belegschaft auf allen Ebenen konfrontiert, so dass die Gewinnung von neuem Personal dringend erforderlich war. Hori Tomoyuki, General Manager der Druckvorstufe, erinnert sich: „Insbesondere in der Plattendruckabteilung, die fünf Mitarbeiter beschäftigte, standen mehrere Leute kurz vor der Pensionierung. Der Plattendruckprozess war vom Druckort getrennt und fast die Hälfte des Plattentransports sowie der Stanz- und Biegearbeiten wurden von Hand erledigt, sodass wir unser Personal aufstocken mussten. Da der Arbeitskräftemangel jedoch allgemein immer chronischer wird, ist der Plattendruckprozess keine leichte Arbeit, sodass es schwierig war, neue Talente zu gewinnen.“
Als Lösung konzentrierten wir uns auf die Automatisierung des Druckvorgangs. Das Projekt wurde ins Leben gerufen, als Eco3, das arbeitsablaufbezogene Produkte verwendet, das Plate Transportation System (PTS) vorschlug.
PTS ist eine automatisierte Lösung, die alles vom Plattenbiegen bis zur automatischen Verteilung an Stapler ermöglicht. Hori besuchte sofort einen bestehenden Benutzer in Tokio und sagte, er sei „beeindruckt, dass dort niemand war“. Er stellte jedoch fest, dass die Automatisierung des Prozesses schwierig sein würde, da das Unternehmen fünf verschiedene Plattengrößen verwendet. Da dadurch jedoch der menschliche Arbeitsaufwand deutlich reduziert würde, der Personaleinsatz optimiert und die vom Menschen verursachten Probleme, die mit der manuellen Arbeit des Stanzens und Biegens von Platten einhergehen, eliminiert würden, beschlossen die Druckvorstufen- und Druckereistandorte einstimmig, diese Technologie einzuführen.
Gab es bei dieser Entscheidung keinen Spielraum für Vergleiche und Überlegungen zu Automatisierungssystemen anderer Hersteller? Shimizu Kazunari, Manager der Prepress Division, erklärt: „Da Eco3-Produkte unseren CTP- und Workflow dominieren, hatten wir fast keine anderen Optionen. Automatisierte Systeme wie PTS werden durch Signale von der Ausrüstung gesteuert, daher sind die Hürden hoch, wenn verschiedene Hersteller gemischt werden. Darüber hinaus ist es schwierig, die Ursache zu ermitteln, wenn Probleme auftreten. Eco3 hat den Ruf, immer innovative Vorschläge zu unterbreiten, wie z. B. PDF-Workflow, Cloud Computing und Abonnementdienste. Unter anderem schlugen sie ein auf unser Unternehmen zugeschnittenes PTS vor, also wollten wir mit ihnen zusammenarbeiten.“
Es wurde tatsächlich im Oktober letzten Jahres installiert. Die Startarbeiten wurden an zwei dreitägigen Wochenenden durchgeführt. Der Ablauf des eingeführten PTS ist wie folgt:
Zunächst werden die von den beiden CTP-Maschinen gedruckten Platten auf einer einzigen Transportschiene zusammengeführt. Mithilfe des QR-Codes lässt sich ablesen, ob die Platte gestanzt und gebogen wurde. Nach jedem Vorgang werden die Auftragsinformationen mit einem Tintenstrahldrucker auf die Rückseite der Platte gedruckt. Abschließend werden die Platten entweder nach Druckmaschine oder nach Vorder- und Rückseite in 10 verschiedene Stapler sortiert.
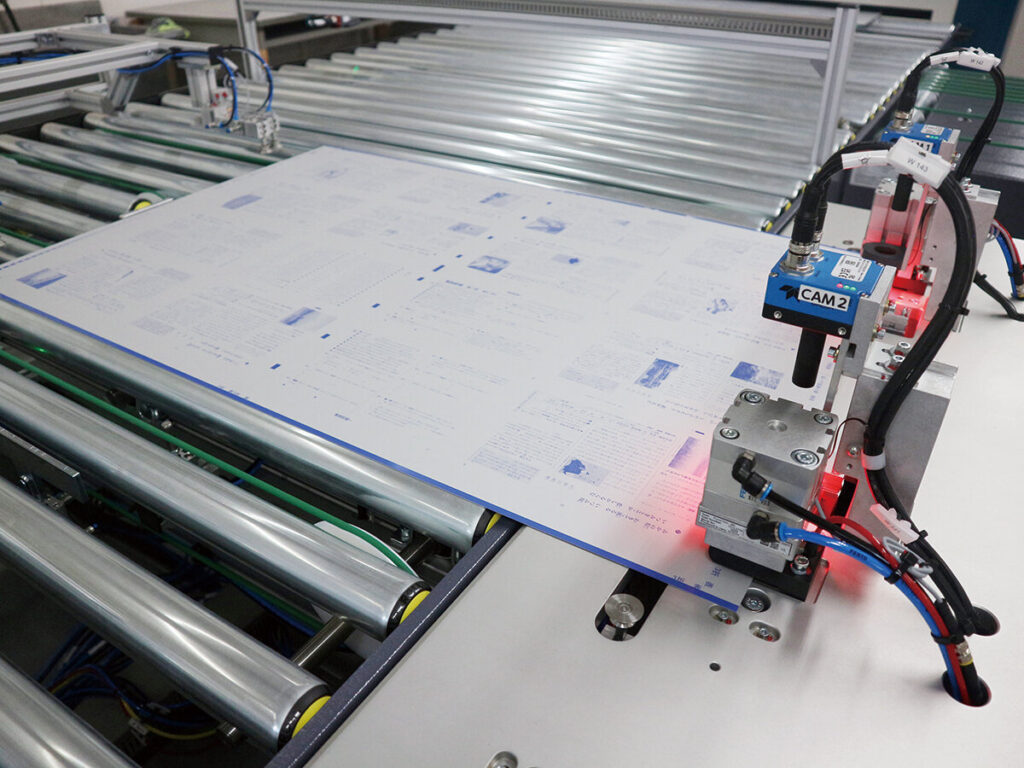
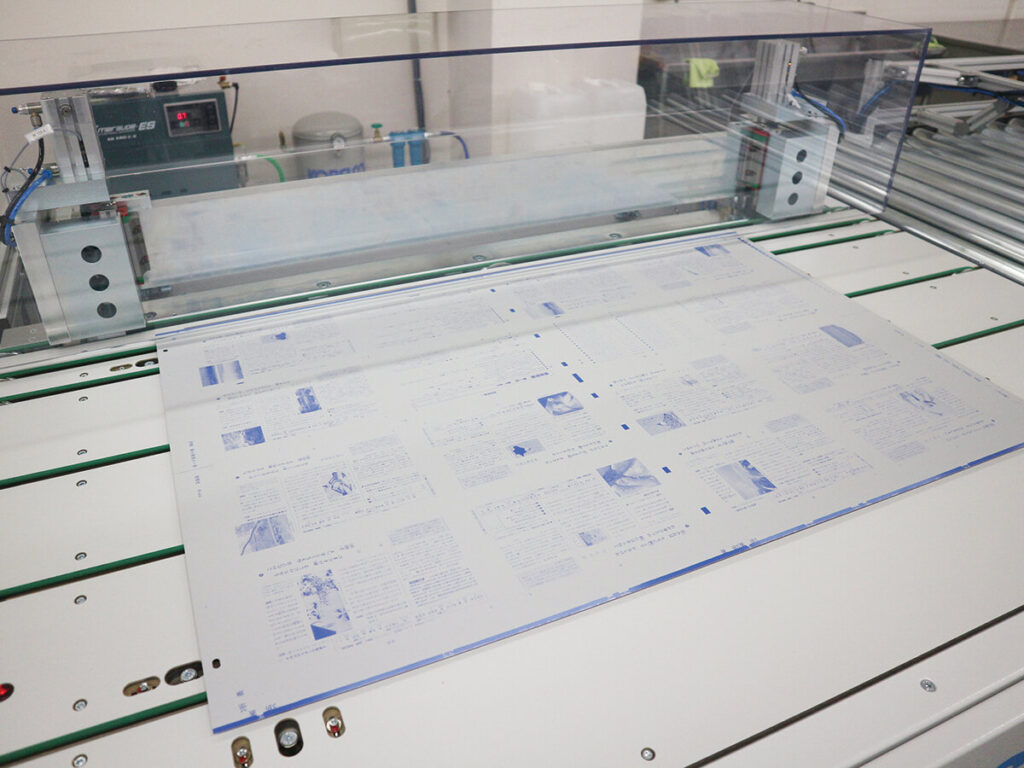
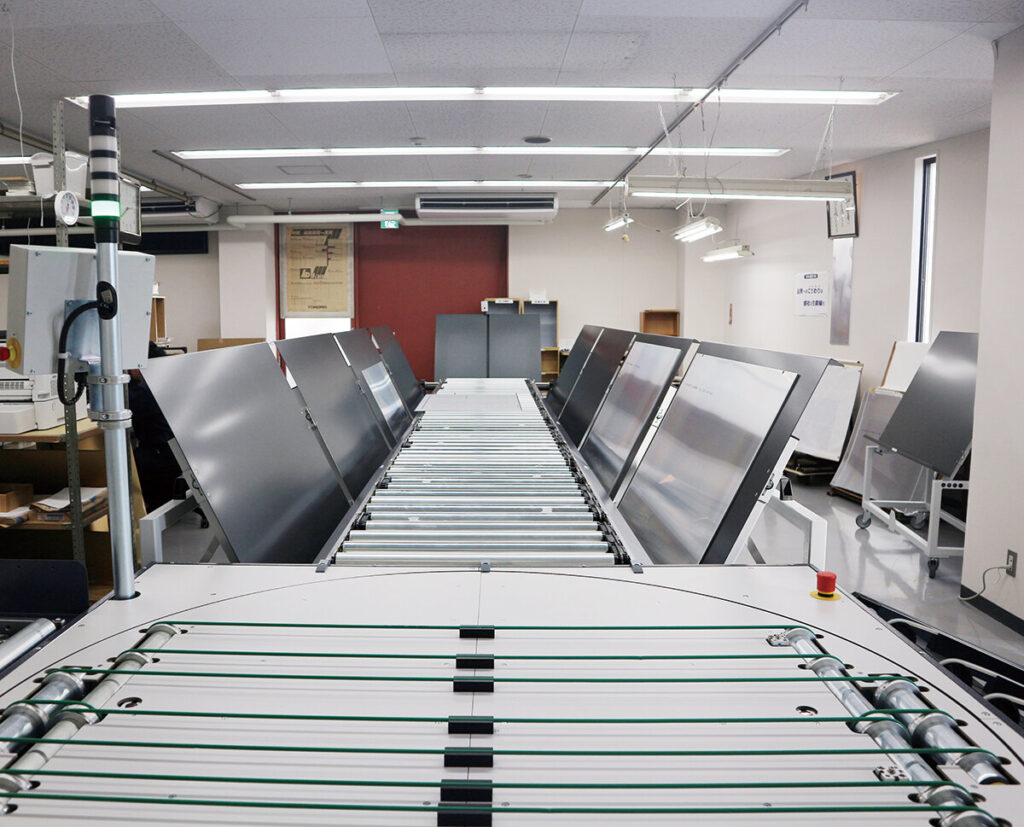
„Unser Unternehmen verfügt über vier Rollenoffset- und vier Bogendruckmaschinen, die wir zudem den einzelnen Subunternehmern zuordnen müssen, sodass 10 Typen nicht ausreichen. Da wir zudem räumliche Einschränkungen haben, lösen wir dieses Problem durch flexible Betriebsabläufe“, so Shimizu.
381 Stunden Einsparung pro Jahr allein durch das Biegen von Platten
Das Unternehmen hat die Automatisierung durch die Integration der folgenden Elemente in seine PTS-Linie erreicht: Spezialstanzungen, die nicht mit den CTP-Innenstanzen verarbeitet werden konnten und manuell durchgeführt werden mussten, die Plattenzuordnung, die aufgrund der großen Anzahl und Vielfalt der Druckmaschinen kompliziert war, sowie das handschriftliche Eintragen von Auftragsinformationen auf die Rückseite der Platten. In der Folge wurde die Mitarbeiterzahl der Druckerei von fünf auf zwei reduziert. Zudem konnte die Berührungshäufigkeit der Platten durch die Mitarbeiter beim Sortieren und Transportieren um 80 % reduziert werden, wodurch es ebenfalls gelang, vom Menschen abhängige Handhabungsprobleme zu vermeiden (siehe Abbildung).
Betrachtet man dies im Hinblick auf die Arbeitszeit, umfasst der Blechbiegeprozess den Transport der Bleche zur Biegemaschine im Blechraum und das Biegen von ungefähr 45.800 Blechen pro Jahr. Bei einem angenommenen Zeitaufwand von jeweils 30 Sekunden ergibt sich eine Einsparung von 381 Arbeitsstunden pro Jahr.
Zusätzlich werden beim Stanzvorgang Platten zur Stanzmaschine im Plattenraum transportiert und gestanzt, wodurch jährlich 10.200 Platten entstehen. Geht man davon aus, dass auch dieser Vorgang jeweils 30 Sekunden dauert, könnte dies zu einer Arbeitszeitersparnis von 85 Stunden pro Jahr führen.
Wenn es darüber hinaus um das Schreiben von Auftragsinformationen geht, wird dieser Wert auf Null reduziert, wenn man davon ausgeht, dass für das handschriftliche Schreiben von 100.000 Kopien pro Jahr jedes Mal 20 Sekunden benötigt werden, was zu einer Reduzierung der Arbeitszeit um 555 Stunden führt.
Yamazaki Shota, stellvertretender Leiter der Druckvorstufenabteilung, erläutert die Auswirkungen des Systems wie folgt: „Bis jetzt bedeuteten die Stanz- und Biegearbeiten manchmal Überstunden oder mussten auf den nächsten Tag verschoben werden, auch wenn wir die Druckplatten innerhalb der Arbeitszeit fertigstellen konnten. Jetzt können wir alles innerhalb der Arbeitszeit fertigstellen und es gibt keine Probleme mehr wie Kratzer. Wir haben die gewünschten Auswirkungen der Einführung erzielt, indem wir die Anzahl der Mitarbeiter reduziert, die Arbeitszeit verkürzt und Plattenprobleme eliminiert haben.“
Bei solchen automatisierten Systemen kommt der Unterstützung im Problemfall eine enorme Bedeutung zu. Wie wird Eco3 reagieren?
„Natürlich gab es einige kleine anfängliche Probleme, aber die Kommunikation mit dem PTS-Hersteller über Eco3 Japan verlief stressfrei und das Feedback kam schnell. Programmänderungen wurden per Fernzugriff direkt von Deutschland aus abgewickelt, sodass es keine besonderen Zeitverzögerungen gab“, sagte Shimizu.
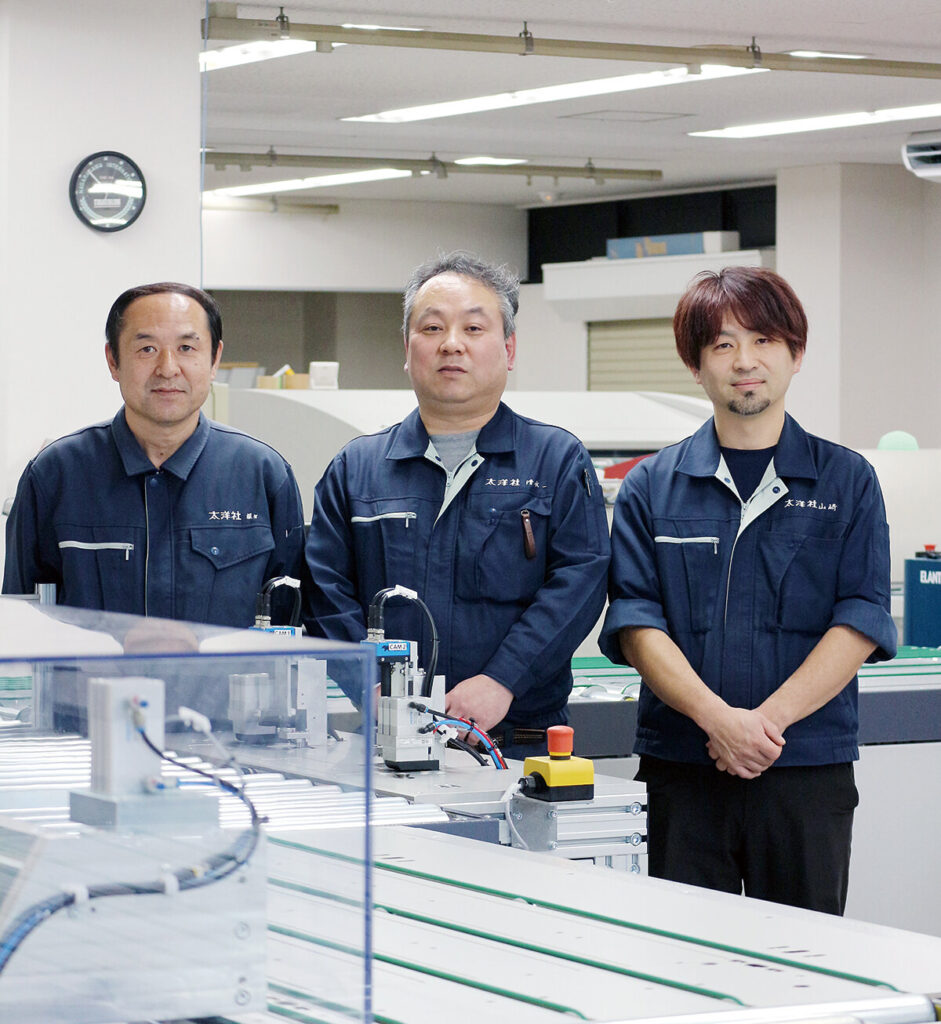
Expert Loader für noch mehr Effizienz
Zu der Möglichkeit weiterer Effizienzsteigerungen in der Zukunft sagte Abteilungsleiter Shimizu: „Die CTP-Ausgabeabteilung liegt gegenüber der Druckerei auf der anderen Seite einer Nationalstraße, daher ist diese physische Distanz schwer zu überwinden, aber ich denke, dass wir sie je nach Betriebsweise möglicherweise auf ein Ein-Bediener-System reduzieren können.“ Es scheint auch eine Option zu sein, den Expert Loader (ein automatisiertes CTP-Palettenladesystem, das 1.200 Platten gleichzeitig laden kann), der derzeit nur auf einer CTP-Einheit installiert ist, zu verbessern oder zu erweitern. „In Zukunft möchten wir daran arbeiten, die Effizienz der Plattenherstellungs- und Satzprozesse, einschließlich der Ausschießarbeiten, zu verbessern und den erforderlichen Personalbestand zu reduzieren“, sagte Shimizu.
Am Ende des Interviews sagte Präsident Daido Folgendes über die Ausrichtung seines Unternehmens für die nahe Zukunft:
„Ob man Investitionen tätigen kann oder nicht, wird in ein paar Jahren einen großen Unterschied machen, und Letztere werden ausgesondert werden. Der Markt für Papierdruck wird schrumpfen, aber die Zahl der Druckereien auf der Angebotsseite wird noch stärker schrumpfen. Ich bin überzeugt, dass, wenn es unser Unternehmen in 10 Jahren noch gibt, eine rosige Ära anbrechen wird. Um bis dahin durchzuhalten, werden wir weiter in die Agrarindustrie und andere Bereiche diversifizieren und gleichzeitig systematisch Investitionen tätigen, darunter auch in die Automatisierung.“